Roof Flashing Basics
- Frontline Team
- Dec 17, 2019
- 3 min read
Updated: Nov 26, 2021
You may have heard the word 'flashing' used in the context of roofing and exteriors. But even if you haven't, you're not alone. Our customers often ask us what it is and why it's needed. Unfortunately, it has been a frequent oversight among fellow estimators and contractors when scoping out the necessities of a project.
Typical masonry chimney flashing, pictured above. These aluminum profiles are fabricated onsite to fit each unique chimney.
Defining Flashing - What is it?
Our definition: a waterproof material (usually metal) used and installed in such a way as to shed water and prevent infiltration at protrusions, obstructions or transition points on a roof or exterior of a building. Flashing is primarily for function but may also be considered an aesthetic or cosmetic finishing.
Wikipedia's definition:
Flashing refers to thin pieces of impervious material installed to prevent the passage of water into a structure from a joint or as part of a weather resistant barrier system. In modern buildings, flashing is intended to decrease water penetration at objects such as chimneys, vent pipes, walls, windows and door openings to make buildings more durable and to reduce indoor mold problems. Metal flashing materials include lead, aluminium, copper,[1] stainless steel, zinc alloy, and other materials.
Wikipedia article linked here.
In other words, it’s not optional.
When it comes to flashing, the possibilities are as endless as there are numerous styles of building design and construction. To simplify, it helps to reduce flashing to two basic categories, and they are:
Base Flashing
Counter Flashing (alternatively called a cover/cap flashing)
In the context of a roof, the base and counter flashing both work together. The base flashing will shed water that is channeling down the surface of the roof. This could be along walls, skylights, pipes, chimneys, and so on. The counter flashing serves to shed water that is traveling down the protrusion, obstruction or transition (i.e. water running down the bricks of a chimney). Commonly in the Sudbury area, we see aluminum used as a metal of choice for most residential flashing, with steel being most common on the commercial/industrial side.
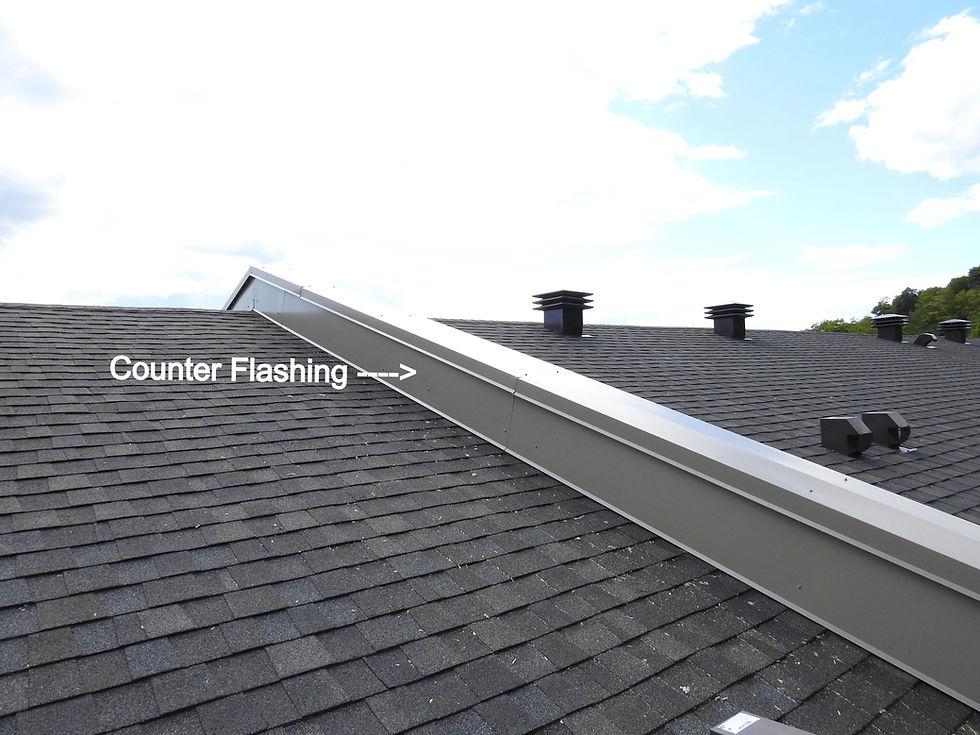
Fabrication and Installation - How is it done?
The tool of choice to fabricate any metal flashing is a large clamping jaw called a brake. This clamp is fed an aluminum sheet from a rolled coil and is used to bend the aluminum sheet to whatever shape and profile is necessary for the job. Flashing profiles vary greatly and they are generally custom made for each project. For example, an ’L-shaped’ flashing may fabricated to be used along where the roofline meets the side of a wall.
Installation methods vary, but the one thing that must always be true of any effective flashing installation is: it has to shed water to protect against water infiltration. A flashing cannot pool or catch water. For example, on a sloped roof, a base flashing must be made and installed in a manner that allows water to freely flow toward the bottom edge and off of the roof. This means that, whenever possible, a flashing must be:
lapped over the roofing materials below it and
lapped under the roofing materials above.
This correct lapping order is essential and ensures that water will travel around and past any protrusion, obstruction or transition without the unreliable (and unappealing) use of sealants like tar or caulking. Sealants used are generally more for the protection of a joint or as an additional preventative measure, not usually as a primary barrier. Metal flashing may be fastened in place with screws, nails or anchors.
We hope this information is helpful for you. We plan to expand more on this topic and discuss in-depth specific types of flashing and how they work.
Feel free to get in touch with us to discuss your project!
❤️